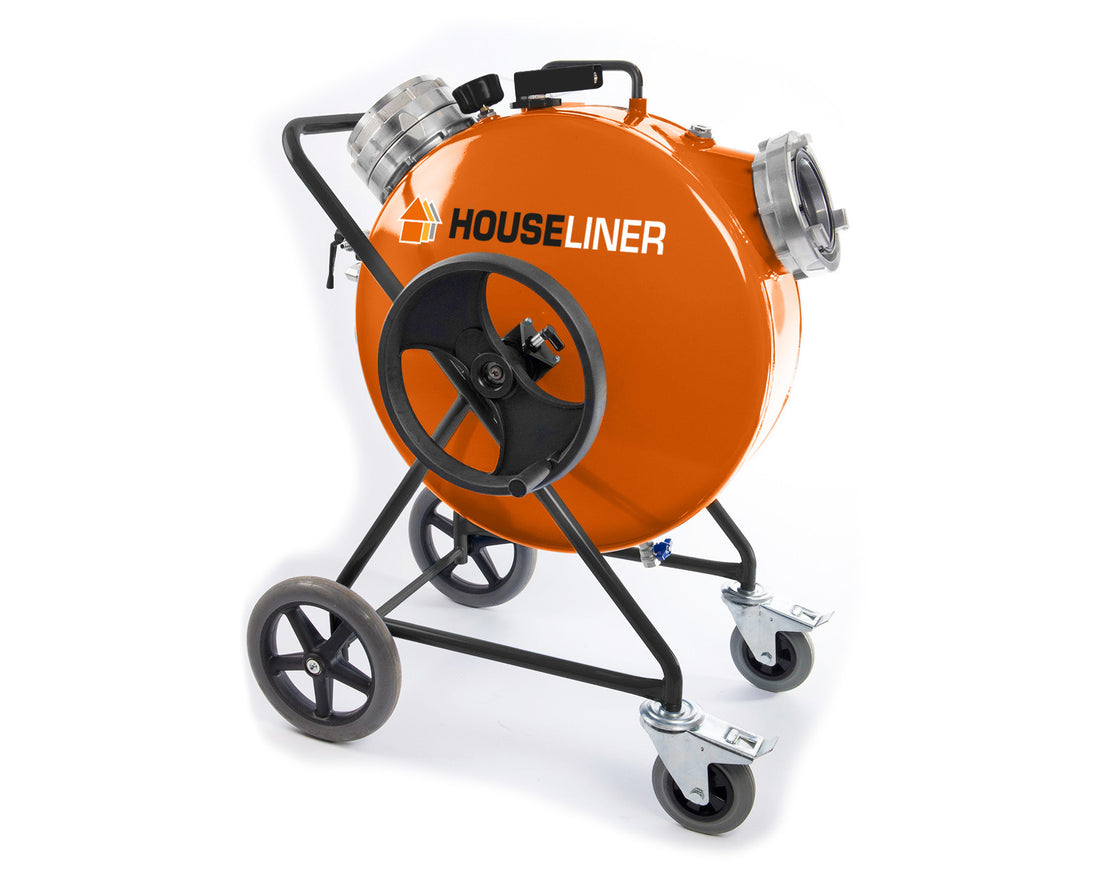
Guide to Getting Started in Pipe Lining for Pros
Share
The field of wastewater network rehabilitation has been revolutionized by pipe lining. This technique, which is both economical and sustainable, avoids the need for major and costly work. For professionals, mastering lining and its stages is crucial to ensuring the longevity of installations.
Faced with constant advances in techniques and materials, lining is emerging as the preferred solution for repairing pipes. Thanks to the use of epoxy resins or reinforced fiberglass sheaths, this method guarantees optimal strength and impermeability. Moreover, lining is a less invasive alternative than completely replacing the pipes.
Understanding Pipe Lining
What is pipe lining?
Pipe lining is a modern technique for the rehabilitation of wastewater networks, without the need for excavation. It involves the use of a sheath - usually made of fibreglass or felt - impregnated with a resin, such as epoxy or polyester. This sheath is inserted into the existing pipe. Following this, the resin solidifies, creating a new, robust and impermeable internal wall. This process helps to extend the life of the pipe, avoiding the disadvantages associated with traditional repairs.
Particularly suitable for pipes that are difficult to access, the lining can be applied to pipes of various dimensions, ranging from 15 to 125 cm in diameter. It is effective in repairing cracks, holes and defective joints. In addition, it can be used to reinforce pipes eroded by corrosion or wear.
The procedure begins with a precise assessment of the duct, using an endoscopic camera. This diagnosis is followed by intensive high-pressure cleaning, thus preparing the surface for the insertion of the resin sheath. The latter is positioned either by traction or by inversion, before being hardened to form the new internal wall.
Advantages of the lining method
Pipe lining has several notable advantages over traditional methods. First, it is more economical, avoiding the costs and disruptions associated with excavation and replacement of pipes. This method also stands out for its speed of execution and its low nuisance for local residents.
In the long term, a sewerage network restored by lining can reach a longevity of 50 years, thus offering a sustainable solution. Its low environmental impact, due to the absence of waste generated by digging operations, is another positive point.
In addition, the lining helps improve water quality. It prevents contamination by infiltration and limits the formation of scale and other plugs, optimizing the overall performance of the sanitation network.
Different techniques and materials used
The field of pipe lining uses a variety of techniques and materials, each suitable for specific contexts. Epoxy, polyester and vinylester resins are preferred for their optimum adhesion and strength once cured.
Depending on the type of pipe and the nature of the problem, the lining methods differ. Continuous fiberglass lining, with polyester resin, stands out for its ability to form a strong, wrinkle-free cover. While epoxy resin-impregnated felt remains ideal for more complex configurations.
Polymerization, essential for the solidification of the resin, varies depending on the material: this process can be done dry, or with the addition of steam, hot water, or UV rays. This step is crucial to ensure the resistance and impermeability of the new internal structure.
Equipment required for pipe lining
Main tools and machines
Pipe lining is a procedure that requires a range of specialist equipment. Milling robots are essential for removing blockages and smoothing internal surfaces. Inspection cameras are equally essential, providing a detailed view of the condition of the pipes to accurately guide the lining.
Resin spraying equipment, such as the CuraFlow® system, ensures a uniform application of the resin. In the case of sleeving, the use of polyester or fiberglass sleeving, impregnated with resin on site, is common practice.
Concerning polymerization, a crucial stage that ensures the hardening of the resin, various equipment is used. These vary according to the technique used: heating systems, use of steam, hot water, or even UV lamps are all solutions for activating and hardening the resin.
Choosing the Right Hardware for Different Types of Pipes
The choice of materials for lining varies depending on the type of pipe and its condition. PVC pipes benefit from resins specially designed for optimal adhesion. As for metal pipes, they often require epoxy resins, known for their resistance to corrosion.
The diameter and configuration of the pipes also influence the selection of materials. Flexible fiberglass conduits are ideal for winding routes, while more rigid versions are suitable for straight sections.
Using specialists is crucial for an informed choice of equipment. They provide personalized recommendations based on the specifics of the site and the characteristics of the pipelines.
Initial investments and maintenance management
Although the initial acquisition of lining equipment represents a significant investment, it pays off in the long run by preventing costly pipe replacements. The main investments are milling robots, resin jetting systems and curing equipment.
Methodical maintenance is essential to extend the durability and ensure the efficiency of the equipment. Regular checks as well as technological updates are essential to keep equipment operational.
Investment in staff training is also a priority. It is essential that operators are competent in modern lining techniques and the proper use of equipment, thus ensuring excellence and safety in interventions.
Setting up a lining operation
Preparatory steps: Inspection and cleaning
To ensure the success of any lining operation, a thorough inspection of the pipes is essential. Using a dedicated camera, this initial analysis makes it possible to identify cracks, obstructions and various damages. Thus, the condition of the pipes is clearly defined, facilitating precise planning of the intervention.
The cleaning step is crucial. It aims to carefully prepare the internal surface for better adhesion of the resin. To this end, high-pressure cleaning is often used to remove debris and various accumulations. This is followed by complete drying, ensuring perfect adhesion of the resin.
The use of personal protective equipment is mandatory to keep technicians safe. This includes thick gloves, masks, goggles and special suits.
The coating process: From preparation to polymerization
The process begins with the careful preparation of the epoxy resin, adapted to the specific needs of the project. The sheath, saturated with this resin, is introduced into the pipeline. The insertion method, by inversion or traction, depends on the specificities of the project.
The polymerization phase follows, where the resin is hardened, creating a tough inner layer. This hardening can be accelerated by various means, such as steam, hot water, or UV, depending on the nature of the resin.
Once hardened, the resin establishes a new, solid internal barrier. This significantly strengthens the pipe, making it both strong and watertight. It therefore increases the longevity of the structure and effectively prevents leaks.
Control and validation of the intervention
A rigorous post-intervention examination is carried out to ensure the quality of the work provided. This step includes a video inspection to confirm the perfect impregnation of the resin and the waterproofing of the rehabilitation.
Functional tests are then conducted. They make it possible to verify that the rehabilitated system operates as expected. These checks concern the flow rate and pressure, ensuring the proper functioning of the pipeline.
Finally, a detailed report is produced. It summarizes the work carried out and the final state of the pipes. This document is crucial for traceability and serves as a valuable reference for any future intervention.
Conclusion
Pipe lining is now an essential method in the renovation of wastewater networks. This technique is distinguished by its durability, affordable cost and less invasive approach compared to conventional methods.
Choosing the right equipment, while carefully following the steps from initial inspection to final assessment, guarantees a significant improvement in the durability of your equipment. This is the ideal time to integrate liner into your future refurbishment projects.
Embrace this evolution in pipeline maintenance and see for yourself its undeniable benefits.